Que cherchez-vous aujourd'hui ?
Entrer votre recherche et appuyez sur « Entrée »
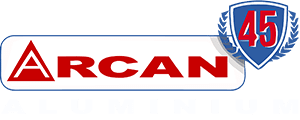
514-331-0062
An aluminum brake bends metal flashing and trim with precision, crucial for siding and roofing projects. Explore the top models in this guide to help you choose the best aluminum brake for your needs. As your trusted construction materials supplier, we can guide you to the best products to help you achieve your renovation goals.
Aluminum brakes play a critical role in the shaping of metal flashing and trim, essential for tasks involving siding and roofing. These tools are relied upon by siding contractors and roofers to mold precise metallic forms that ensure a flawless fit and finish. They stand as pivotal components within the construction sector due to their ability to deliver both accuracy and efficiency required for superior outcomes.
Constructed to manipulate a variety of metals such as aluminum, galvanized steel, and copper, these brakes offer adaptability across various undertakings. Their capability is equally beneficial on industrial construction grounds or during at-home DIY endeavors where meticulousness in metal bending is paramount.
Available in numerous models, aluminum brakes serve an array of users from professional tradespeople to avid home improvements. They bolster work rate while guaranteeing robust installations that meet aesthetic standards reliably.
Contemporary aluminum brakes have undergone substantial improvements, with new designs and technologies that elevate their performance and lifespan. These upgrades result in tools that are not only lighter and easier to manipulate, but also maintain their robustness. Improved casting methods along with surface treatments boost the efficiency and exactness of these devices, rendering them indispensable for tasks in metalworking and construction.
In the realm of recent enhancements, modern aluminum brakes now boast innovative castings as well as sophisticated clamping systems. Such attributes guarantee enhanced proficiency when performing strenuous bending operations without compromising precision.
Focusing initially on the progress made within casting technology, let’s delve into some notable characteristics more comprehensively.
Modern aluminum brakes have been significantly enhanced by the adoption of new and improved castings. The semi-solid casting method affords greater precision in the manufacturing process, leading to fewer imperfections and better qualities of materials. As a result, these components possess reduced porosity which bolsters their dependability and efficacy when subjected to bending operations.
The implementation of advanced castings also elevates thermal conductivity, facilitating superior heat distribution during use. This preservation of material integrity ensures uniform outcomes.
Companies are pivoting towards modular designs that support tailoring and expansion to meet various requirements and uses. These advancements not only boost the functionality of aluminum brakes, but also augment their durability and overall user satisfaction.
Shifting away from the old-style hinge systems to cam locking systems has led to a substantial enhancement in aluminum brake technology. Some brake models utilize an innovative cam locking system, which offers an upgraded and more reliable locking method over conventional hinges. This advancement guarantees that materials are firmly held in place while bending, improving both performance and user convenience.
Consequently, operators encounter less trouble with materials slipping or becoming misaligned. This change contributes to achieving bends that are both more accurate and consistent.
Robust clamping systems, like the Power Lock. Bars utilized in contemporary aluminum brakes are essential for attaining precise and consistent bends when working with aluminum materials. These strong clamping mechanisms guarantee that during bending, the material is held firmly in place. This not only improves bend accuracy but also preserves the material’s condition to prevent damage and assure superior quality outcomes.
These advanced clamping systems bring added value due to their increased durability and capability to endure demanding operations. Their strength plays a pivotal role in delivering reliable performance over time.
The market is saturated with a variety of aluminum brakes that cater to distinct requirements, featuring exclusive attributes and benefits.
Although each model has its own distinctive advantages, Tapco brakes distinguish themselves through their advanced design features and functional versatility, earning them significant recognition in the marketplace.
Dedicated to ease-of-use while managing intricate bending profiles effectively adds another layer of utility making it quite adaptable within its product category. Let’s delve deeper into what the Tapco brakes offer enthusiasts in this field.
Tapco brakes stand out in the market as a top choice, renowned for their advanced lightweight construction and cutting-edge design. They are equipped with an exclusive moving pivot hinge that boosts bending capabilities, facilitating effective metalworking while maintaining robustness.
Owing to their light build, Tapco brakes offer ease of transportation and maneuverability. This combination of easy handling and high efficiency makes them highly favored among contractors who value both mobility and powerful performance. Learn about why the Tapco brakes are highly recommended.
Gaining proficiency in numerous metal bending methods is crucial for fabricating exact metal forms necessary for roofing and construction projects. Utilizing aluminum brakes offers the versatility to produce bespoke metal profiles, which can lead to improved accuracy and effectiveness. These techniques encompass a variety of applications from crafting straightforward flashing details to constructing intricate outside corner posts along with complex bending profiles, all necessitating distinct strategies and settings.
Ensuring efficiency when operating aluminum brakes involves meticulous preparation combined with selecting the right tools. Opting to measure bend locations on-the-fly as opposed to each time individually rather than relying on pre-marked measurements can enhance precision while also saving time.
We shall delve into various prevalent bending techniques more thoroughly, examining their particular uses within this field.
The process of bending simple flashing entails readying the material, calibrating the aluminum brake to a specific angle, and performing a smooth bend to prevent any kinks. This step is essential for making sure that the flashing aligns flawlessly and yields an aesthetically pleasing end result. More accurate bends can be obtained by taking measurements for each bend location on its own rather than marking them beforehand, which contributes to achieving more precise outcomes.
When hemming metal flashing one must firmly place the metal within the brake mechanism then lock it in position before flexing it upwards to forge a neat edge.
Precise bends are necessary to ensure the aesthetics and functionality of intricate outside corner posts, which requires careful measurements and controlled bending for preserving the design. To prevent any distortions and attain the correct form, it is crucial to apply consistent pressure throughout the bending process.
To achieve accurate bending that maintains design integrity, employing a bending brake with an efficient hinge mechanism is key. This tool aids in forming exact angles critical for both appearance and practical application of these corner posts.
Effectively managing complex bending profiles requires a clear grasp of the unique needs associated with each profile and tailoring the settings on the brake appropriately to achieve desired outcomes. Overbending is frequently required as a countermeasure for material spring back, which guarantees that the final form aligns with specified targets.
Comprehension of individual profile necessities combined with employing overbending techniques are critical for successfully handling complex bending profiles.
Utilizing aluminum brakes may come with a variety of hurdles, yet grasping these problems along with their respective solutions can considerably enhance the caliber and productivity of manufacturing processes. Owing to differences in strength and flexibility, each type of aluminum alloy necessitates its own specific method for bending. Common obstacles that must be dealt with include compensating for an increased bending radius to achieve accurate outcomes and rectifying issues related to overbending.
To combat these challenges effectively, strategies such as reinforcing broad trim sections with ribs can prevent warping while enhancing the final product’s visual appeal. Adopting protective measures like adequate guarding and implementing dual-hand controls are vital steps in reducing potential harm during the operation of aluminum brakes.
Exploring these aforementioned difficulties along with their solutions more thoroughly will provide a better insight into managing them effectively.
Excessive bending during the forming process can result in major flaws, including cracks and wrinkles on aluminum components. These problems arise from too much stretching, especially in thicker sheets of aluminum where over-bending is likely to lead to cracking or distortion.
It’s crucial to keep the bend radius appropriate for the thickness of the material being used in order to mitigate issues related to over bending. By doing this, you can avoid surface imperfections and achieve outcomes that are of superior quality.
It is essential to account for an increased bending radius in order to preserve the accuracy of aluminum bending operations. Variations in the curvature of molds and fluctuations in the quality of materials can cause profile contour discrepancies.
By continuously checking material quality and frequently modifying the bending configuration to suit a greater radius, one can achieve precise and reliable results.
Aluminum alloy series such as 3xxx, 5xxx, and 6xxx are favored for bending tasks because of their superior formability. To achieve the best results in forming aluminum components, they should be bent while in a softened (annealed) state before being heat-treated (tempered), which minimizes the risk of cracking during the bending operation.
In cases where tempered aluminum alloys like 6061-T6 need to be bent, it is essential to either employ greater inside bend radii or execute a series of incremental bends to avoid cracks from developing.
Advancements in aluminum brakes have redefined their functionality, boosting not only performance but also longevity and user-friendliness. Contemporary designs commonly incorporate dual pivot hinges, which amplify the force and effectiveness of bends, rendering these brakes adaptable for a multitude of tasks. This progress aptly harmonizes performance with durability while considering cost-effectiveness to deliver maximum return on investment.
The incorporation of sophisticated technologies such as auto measure systems alongside enhanced casting methods has been pivotal in transforming the sector. Such improvements optimize workflow efficiency by minimizing idle times and elevating both precision and consistency in bend outputs.
We shall delve deeper into some of these avant-garde attributes that mark today’s cutting-edge innovations.
The incorporation of auto measure technology into aluminum brakes has markedly improved their capabilities by enabling the automatic execution of measurements and adjustments. This innovation diminishes the need for time-consuming manual configurations, thereby boosting productivity. Automation in measurement ensures decreased downtime and enhanced accuracy, leading to more effective and dependable operations for users.
Advancements in casting technology have resulted in the production of components that are simultaneously stronger and lighter. This progress has delivered aluminum brakes with enhanced durability and performance capabilities while being easier to manage, achieving similar or superior effectiveness compared to previous versions.
These improved castings not only bolster the strength of these instruments, but also significantly extend their lifespan and dependability when applied in real-world settings.
Pioneering firms have been pivotal in the evolution of aluminum brake technology, incorporating auto measure features that streamline processes and bolster precision for operators.
These inventive enterprises have driven enhancements in performance and facilitated a shift from conventional hinge systems to cam locking mechanisms. This transition has yielded superior functionality and user-friendliness. Their dedication to refining strong clamping designs guarantees accurate bending angles, thus improving the quality of outcomes for their clientele.
Adhering to effective tips and adhering to best practices can greatly enhance the advantages of using aluminum brakes. It’s essential to focus on correct setup and choosing the right tooling, which is key for achieving accurate bends in aluminum flashing. Mastery over operational methods along with a keen awareness of safety protocols improves both performance and durability of these instruments. Consistent maintenance coupled with proper usage techniques guarantees superior outcomes while preventing typical problems.
Integrating these strategies into your daily workflow boosts both productivity and dependability when working with aluminum brakes, leading to excellent quality finishes in your work. We will delve into some specific recommendations shortly.
Ensuring the longevity and efficient performance of aluminum brakes hinges on consistent upkeep. Diligent examinations for signs of deterioration help avert unforeseen breakdowns while optimizing their function. It’s crucial to maintain cleanliness and proper lubrication of these tools to prevent corrosion and promote better operation.
The use of templates in crafting intricate profiles is instrumental, as it facilitates experimentation and refinement before manufacturing the final product, thus guaranteeing accuracy.
To avoid injuries and guarantee seamless operations, it is crucial to adhere to safety measures when operating aluminum brakes. Don’t wear protective gloves at all times to safeguard against cuts from the metal’s sharp edges. The implementation of appropriate guarding and dual-hand controls can significantly diminish the potential for harm while in use.
Adherence to these precautionary steps will foster a more secure work setting, thereby curtailing the likelihood of mishaps.
Utilizing advanced technologies and fine-tuning operational methods is key to maximizing efficiency when working with aluminum brakes. Technologies such as auto measure enable automatic calculations and modifications during the bending operations, streamlining the process of measurement. This considerably cuts down on setup time, leading to a boost in productivity.
Incorporating these instruments and methodologies allows you to obtain quicker and more accurate results in your metalworking endeavors.
Various aluminum brake accessories have been developed to augment the capabilities of aluminum brakes, improving both their efficiency and precision during bending processes. The inclusion of tools like trimmers, multi-gauges, trim cutters, and coil dispensers is instrumental in ensuring more precise measurements are attained. To facilitate cleaner cuts, they also optimize material management. Consequently, these enhancements prove to be essential for any complete aluminum brake system.
Incorporating such accessories into your metalworking arsenal can significantly boost your operational prowess when working with metals. This investment not only enhances the quality of output on projects, but also ensures that superior outcomes are consistently achieved.
To encapsulate, aluminum brakes have become indispensable for creating exact metal configurations in the siding and roofing industry. Recent innovations have resulted in tools that are not only more lightweight and potent, but also significantly more adept at their job, boasting features such as enhanced castings, sophisticated cam locking systems, and powerful clamping mechanisms. Renowned models like Tapco’s line of brakes offer specialized advantages to meet various professional requirements. By understanding these essential attributes alongside typical hurdles and effective usage strategies, you can make educated choices that will improve your metalworking endeavors. Seize these technological advancements to advance your craft skills exceptionally.
Modern aluminum brakes include enhanced castings, advanced cam locking systems, and robust clamping mechanisms, ensuring superior performance and durability.
Issues frequently encountered with aluminum brakes encompass the propensity to overbend, resulting in imperfections and also necessitate compensation for an augmented bending radius alongside variations in material attributes.
It is imperative to tackle these challenges to guarantee efficient and precise performance of the brake system.
Recent innovations in aluminum brakes focus on auto measure technology, enhanced casting techniques, and advancements from innovative companies that improve performance and usability.
These developments reflect a commitment to enhancing brake efficiency and reliability.
To optimize aluminum brakes, prioritize regular maintenance, adhere to safety precautions, and utilize auto measure technology.
These practices will enhance performance and ensure safety.